Комплексные технологии внепечной обработки чугуна и стали
Комплексные технологии внепечной обработки чугуна и стали.
Возможности получения стали той или иной степени чистота существенно различаются для электросталеплавильных агрегатов и конвертеров (мартеновские печи занимают промежуточное положение). Конвертерное производства имеет то преимущество, что шихта состоит в основном из жидкого чугуна, не содержащего обычно примесей цветных металлов в заметном количестве. Иногда для получения особо чистой стали металлошихта конвертеров состоит на 100 % из чугуна. Однако чугун содержит некоторое количество таких нежелательных примесей, как фосфор и сера. Вместе с тем современное металлургическое производство располагает технологиями, обеспечивающими весьма эффективную обработку жидкого чугуна перед подачей его к сталеплавильным агрегатам. Целью внепечной (внедоменной) обработки чугуна является его десульфурация, дефосфорация и обескремнивание. В отдельных случаях осуществляется дополнительный подогрев чугуна.
Внедоменная десульфурация чугуна. В качестве реагентов-десульфураторов при внепечной обработке чугуна используют магний (в виде чистого магния, смеси извести и магния, в виде кусков кокса, пропитанных магнием, в виде гранул магния, покрытых солевыми покрытиями и др.), кальцийсодержащие материалы (в виде извести, известняка, карбида кальция) и соду. Основные реакции десульфурации чугуна:
Mg + [S] = MgS; СаО + [S] + О = CaSг + СОг; СаС2 + [S] = CaS + 2С; Na2O + [S] + С = Na2S + СОг; ΔG01 = - 104100 + 44.07 Дж/моль; ΔG02 = 25320 - 26,33 Дж/моль; ΔG03 = - 86900 + 28,72 Дж/моль; ΔG04 = - 2000 - 26,78 Дж/моль.
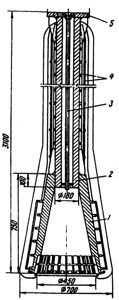
|
|
Рис. 1 Фурма для ввода магния в чугун: 1 - испарительная камера с отверстием для выхода ларов магния; 2 - несущая труба; 3 - канал; 4 -стальная арматура (покрывается огнеупорной обмазкой); 5 - фланец |
|
Расчеты показывают, что для связывания 1 кг серы необходимо 0,75 кг Mg, 1,75 кг СаО, 2 кг СаС2, 3,31 кг CaСО3. Наиболее низкий расход реагентов - в случае использования металлического магния; при этом обеспечивается высокая степень десульфурации. К преимуществам использования магния можно отнести такие факторы, как малое количество образующегося шлака и то, что в процессе десульфурации магнием практически не образуется продуктов, вредных для окружающей среды. Однако стоимость магния сравнительно высока, и выбор реагента определяется в конечном счете экономическими соображениями.
Ввод реагентов в металл может осуществляться в виде кусков, гранул, порошков, проволоки. При вдувании порошков в качестве несущего газа используют воздух, азот, природный газ. Перемешивание реагентов с металлом можно осуществлять различными способами, в том числе: 1) падающей струёй металла; 2) различными механическими мешалками; 3) барботажем под воздействием продувки газом; 4) пульсирующей затопленной струёй и другими способами (воздействием вибрации, ультразвука, газлифтным перемешиванием).
Работа с магнием имеет свои особенности, связанные, во-первых, с тем, что магний при нагреве до расплавления испаряется, объем его возрастает в тысячи раз и, во-вторых, энергия взаимодействия паров магния с примесями жидкого металла и с окружающим воздухом (окисление магния с образованием MgO с выделением большого количества тепла 2Mg + О2 = 2MgO настолько велика, что наблюдается пироэффект в виде яркой вспышки.
Поэтому магний вводят в металл обычно под специальным колпаком-испарителем со щелями для выхода паров магния (рис. 1) или каким-либо иным способом, исключающим выброс жидкого металла (пассивированием кусков магния, заполнением магнием пор в кусках инертного материала, в пористых кусках кокса (рис. 2), введением в чугун гранулированного магния в токе природного газа или азота и т.п.). На рис. 3 показана схема введения в чугуновозные ковши (обычные или миксерного типа) гранулированного магния в токе азота.
При использовании смесей типа известь + плавиковый пшат + реагент, снижающий окисленность ванны (алюминий, кокс и т.п.) используют мешалки (рис. 2). Перемешивание металла с реагентом достигается вращением ротора-мешалки и пропусканием через ротор газа-перемешивателя (обычно азота), создающего эффект кипения. В последнее время все большее распространение получает метод обработки чугуна с использованием проволоки, наполненной реагентами-десульфураторами. Перемешивание массы металла достигается при этом дополнительной продувкой ванны газом (азотом).
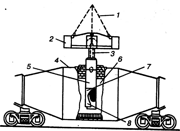 |
Рис. 2. Схема установки для десульфурации чугуна магниевым коксом: 1 - цепной подъемник; 2 - балласт; 3 - стальной вал; 4 - ковш 'Торпедо"; 5 - графитовый стержень; 6 - чугун; 7 - магниевый кокс; 8 - графитовый колокол |
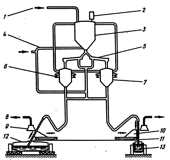 |
Рис. 3. Схема ввода гранулированного магния в чугуновозные ковши: 1 - десульфураторы; 2 - пылевой фильтр; 3 - бункеры; 4 - сжатый воздух (азот); 5 - транспортный желоб; 6 - взвешивающее устройство; 7 - распределитель пылевидных материалов; 8 - пылеулавливание; 9 - пляжной зонт; 10 - тележка фурмы; 11 - погружная фурма; 12 - ковш "Торпедо"; 13 - открытый ковш |
При использовании азота необходимо учитывать протекание реакции 3Мg + N2 = Mg3N2 + Q. Лучшие результаты получают при использовании природного газа, так как в зоне реакции происходит диссоциация метана, снижающая температуру до ~ 1200 °С, что способствует протеканию экзотермической реакции образования MgS. Над поверхностью расплава в ковше создается защитная восстановительная атмосфера, что блокирует поступление кислорода из атмосферы.
Результаты обессеривания при использовании смесей на базе СаО зависят от ряда факторов:
- конструкции ковша (в открытом ковше результаты хуже, чем в ковше миксерного типа, например "Торпедо");
- количества попавшего в ковш миксерного шлака (при значительном количестве миксерного шлака получение низких концентраций серы в чугуне практически недостижимо);
- температуры чугуна (чем выше температура, тем лучше результаты десульфурации);
- содержания в чугуне кремния (чем меньше в чугуне кремния, тем лучше для десульфурации);
- расхода реагентов-десульфураторов. При прочих равных условиях расход зависит от содержания серы в чугуне до обработки [S]нач и требуемого после обработки [S]кон. На рис. 5 показаны принятые на одном из заводов нормы расхода порошка магния, покрытого солью, необходимого для получения чугуна [S]кон < 0,008 % в зависимости от [S]нач.
Хорошие результаты по обессериванию чугуна могут быть получены при использовании соды, однако при обработке содой в атмосферу выделяется большое количество летучих веществ (включая испаряющийся Na2O, образующийся при контакте соды Na2CO3 с расплавленным металлом). Этот метод требует обязательного наличия стендов, оборудованных хорошо действующими пылеулавливающими устройствами, и технологии утилизации уловленных соединений натрия.
Внедомённая дефосфорация чугуна. Для удаления фосфора используют обычно смеси прокатной окалины (или железной руды) с известью и плавиковым шпатом, соду или вдувание извести в потоке кислорода (рис. 5).
При обработке оксидов железа и извести идет реакция
2Р + 3(СаО) + 5FeO = 3СаО - Р2O5 + 5Fe,
а при обработке содой
4[Р] + 5Na2CO3 = 5Na2O·2P2O5 + 5С.
Опыт показал, что при наличии в чугуне кремния введение как оксидов железа, так и соды сопровождается энергичным его окислением
[Si] + 2(FeO) = SiO2 + 2Fe;
[Si] + Na2CО3 = Na2О SiО2 + C;
2[Si] + 2Na2CO3 = 2Na2О + SiО2 + 2CO.
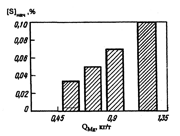
|
|
Рис. 5. Нормы расхода магния
для получения в чугуне < 0,008 % S |
|
Процесс дефосфорации чугуна начинается лишь после удаления кремния. Поэтому во всех случаях, когда проводится операция дефосфорации, ей предшествует проведение обескремнивания.
Обескремнивание и дефосфорация чугуна. Операция внедоменного обескремнивания чугуна позволяет решать следующие задачи: 1) более эффективно использовать реагенты, вводимые для десульфурации и дефосфорации; 2) организовать последующее ведение плавки в конвертере с минимальным количеством шлака ("малошлаковая" или "бесшлаковая" технология). Для удаления кремния обычно используют обработку жидкого чугуна прокатной окалиной или какими-либо иными железорудными материалами, которые вводят сверху на желоб доменной печи или в ковш.
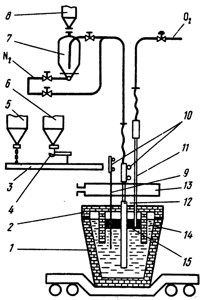 |
Рис. 6. Схема установки для дефосфорации чугуна содой: 1 - ковш; 2 - крышка; 3 - конвертер (подача реагентов без вдувания); 4...6 - питатель и бункеры для соды и окалины; 7 - пневмонагнетатель;8 - бункер; 9 - отбор проб, измерение температуры; 10 - подъемные устройства; 11 - кислородная фурма;12 - фурма для вдувания порошка;13 - зонт для улавливания пыли;14 - металл, 15 - шлак |
В процессе обработки окисляются кремний и углерод:
[Si] + 2/3Р2О5 = SiО2 + 4/3Fe
[С] + 2/3Р2O5 = 2CO + 4/3Fe
Если давление в реакционной зоне заметно меняется и отличается от 0,1 МПа (1 атм.), то равновесие реакции окисления углерода сдвигается влево. Для реакции окисления кремния изменение давления значения не имеет.
Соответствующие расчеты представлены на рис. 7. При подаче реагентов не на поверхность, а в глубь металла под давлением соотношение скоростей окисления кремния и углерода меняется (затрудняются условия удаления углерода); основная доля окислителя расходуется на окисление кремния. Кроме того, повышению скорости окисления кремния способствует барботаж металла при вдувании реагента.
Барботаж ванны и интенсивное при этом ее перемешивание способствуют начинающемуся после обескремнивания процессу окисления фосфора. Использование метода вдувания реагента весьма эффективно при введении в глубь ванны порошкообразной соды; степень полезного использования вводимого натрия при этом приближается к 100 %.
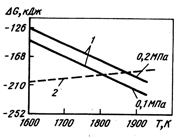 |
|
Рис. 7. Зависимость ΔG от температуры для реакции окисления углерода (1) и кремния (2) |
|
Совместное проведение операций десульфурации и дефосфорации. Как известно, для проведения операций дефосфорации и десульфурации требуются разные условия. Для успешной дефосфорации желательно иметь высокий окислительный потенциал и невысокую температуру, для десульфурации - невысокий окислительный потенциал и повышенную температуру. На рис. 7 представлен один из вариантов решения проблемы организации операций дефосфорации и десульфурации в одном агрегате. В зоне выхода из фурмы, подающей в глубь металла окислительную смесь, окисляется фосфор; на границе раздела металл - высокоосновный малоокисленный шлак происходит удаление серы.
Возможен и другой вариант. В предварительно обескремненный чугун вдувают порошок извести, а через верхнюю фурму обдувают поверхность металла кислородом и таким образом проводят дефосфорацию. Затем отключают кислородную фурму, а для удаления серы вдувают соду. На использующем эту технологию заводе "Kobe Steel" содержание фосфора снижается с 0,080 до 0,010 %, а серы с 0,05 до 0,01 %.
Комплексные технологии внепечной обработки чугуна и стали. Появление новых технологий, способных обеспечить глубокое рафинирование как чугуна, так и стали, позволяет по-новому организовать весь технологический процесс получения стали. Ниже приведено несколько примеров.
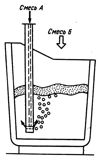 |
|
Рис. 8. Схема рафинирования чугуна от фосфора и серы: смесь а - известь, железная руда (окалина), плавиковый шпат; смесь б - известь и плавиковый шпат |
|
1. На заводе "Kobe Steel' (Япония) предварительно обескремненный чугун заливается в ковш и поступает на установку, оборудованную двумя фурмами, одна из которых предназначена для подачи реагентов в глубь металла. После дефосфорации и десульфурации скачивают шлак, и металл переливают в конвертер для продувки на сталь. Полученную сталь рафинируют на установке ковш-печь, вводят реагенты-десульфураторы и вакуумируют. Такая комплексная технология позволяет получать сталь, содержащую ([Р] + [S]) < 0,005 %.
2. В 1985 г. на заводе "Miwhima Work" (Япония) пущен комплекс, состоящий из оборудования для обескремнивания чугуна на желобе доменной печи и обескремнивания, дефосфорации и десульфурации чугуна в ковше миксерного типа. Для обескремнивания используется смесь агломерационной пыли (75 %) и извести (25 %); смесь для дефосфорации состоит из агломерационной пыли (54 %), извести (38 %), плавикового шпата (4 %) и соды (4 %). Чугун после обработки содержит: < 0,03 % Si; 0,01...0,03 % Р; 0,003...0,020 % S. Все варианты процессов получения чистых по фосфору чугунов включают операции одно- или двукратного скачивания шлака. Такие технологии позволяют получать после продувки в конвертере < 0,0015 % Р в стали.
3. На заводе "Oxelosun" (Швеция) в чугуновозных ковшах миксерного типа производят продувку чугуна смесью СаС + СаСО3 в струе азота; при этом содержание серы снижается с 0,05...0,07 % примерно в десять раз. Для многих марок стали после продувки такого чугуна в конвертере комбинированного дутья внепечная обработка с целью десульфурации не требовалась. Все марки стали на заводе были разбиты на 4 группы (по содержанию серы). Для каждой группы определена своя технология внепечной обработки: для 1-й - "облегченная" обработка жидкого чугуна; для 2-й - "глубокая" обработка чугуна; для 3-й и 4-й групп - внепечная обработка стали.
4. ЦНИИЧМ, ИЧМ, МИСиС совместно с комбинатом "Азовсталь" разработана комплексная технология выплавки в 350-т конвертерах высококачественного металла для толстого листа (с очень низким содержанием серы, фосфора, азота и кислорода и практически без примесей цветных металлов). Технология включает: обработку чугуна в заливочных ковшах магнием в потоке природного газа, обеспечивающую получение в чугуне до 0,002 % S и высокую степень усвоения магния (75...90 %); использование в качестве охладителей конвертерной плавки металлизованных (~ 90 % Fe) окатышей; двухшлаковый процесс со сливом первичного шлака и для предотвращения дефосфорации - слив основной массы конечного шлака при ожидании анализа; загущение оставшейся его части в конвертере и в ковше известью; надежную отсечку шлака в процессе выпуска плавки из конвертера.
Таким образом, развитие методов внепечной обработки чугуна и стали позволяет для каждой группы марок стали выбрать технологию комплексной обработки, включающую одну или несколько операций одновременно (в зависимости от требуемой чистоты стали по фосфору, сере, содержанию газов, примесей цветных металлов, а также в зависимости от затрат на проведение отдельных операций в конкретных местных условиях).
|